work in process inventory balance formula
Ending work in process. WIP Inventory Example 2.
The cost of production rises as inventory in the process increases.
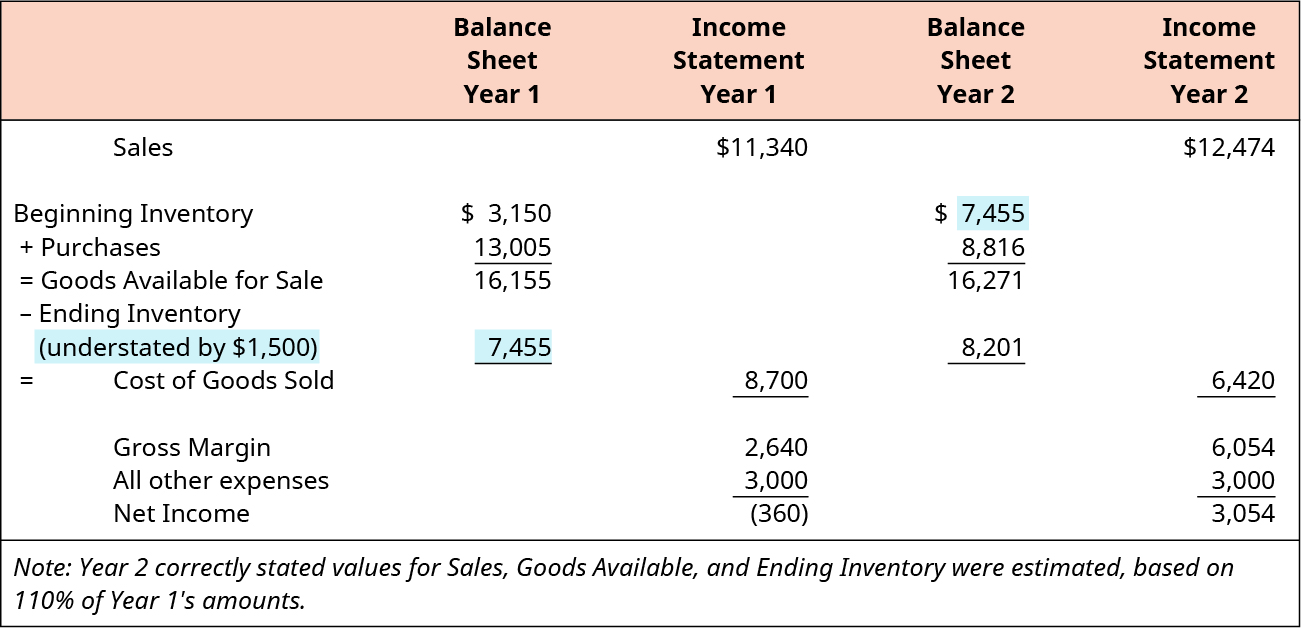
. During the year 150000 is spent on manufacturing costs along with your total cost of finished goods being 205000. From there you would calculate ending WIP inventory amount. If you still need to find your beginning WIP inventory you can do so with a formula.
Deduct the cost of raw material from this figure that is on hand at the end of the accounting period to determine the costs of materials consumed during the accounting period. Regardless of the type of inventory control process you choose decision-makers know they need the right tools in place so they can manage their inventory effectively. Once you know your beginning WIP inventory manufacturing costs and COGM you.
Related
- best hotels in edwardsville il
- hotels in lancaster ca with smoking rooms
- best outlet mall in san diego
- indian fashion jewelry in new jersey
- best easter brunch in savannah ga
- iron rich foods list in hindi
- best bagels in teaneck nj
- beggs funeral home in lincolnton ga
- pet friendly hotels in pleasanton tx
- best in the west shopping center
In this case for example consider any manufactured goods as work in process. Beginning WIP Inventory Manufacturing Costs COGM Ending WIP Inventory. Understanding Work in Process Inventory.
The formula is as followed. Calculate the cost of manufacturing using the work in process inventory formula given below. Any part product or item thats used to make merchandise inventory is listed on a companys balance sheet.
Once you sell the finished goods transfer the. Whether to reference us in your work or not is a personal decision. The amount of ending work in process must be derived as part of the period-end closing process and is also useful for tracking the volume of production activity.
Since WIP inventory takes up space and cant be sold for a profit its generally a best. 30 x 5000 150000. Production costs include raw materials labor used in making goods and allocated overhead.
Work in process inventory includes all raw goods production expenses and labor costs associated with producing merchandise inventory. WIP inventory includes the cost of raw materials labor and overhead costs needed to manufacture a finished product. A work in process or WIP for short is the term that refers to any inventory thats been initiated into production but hasnt been completed by the end of a companys accounting cycle.
WIP is calculated as a sum of WIP inventory total direct labor costs and allocated overhead costs. Work-in-process is an asset and so is aggregated into the inventory line item on the balance sheet usually being the smallest of the three main inventory accounts of which the others are raw materials and finished goods. Your cost of finished goods is.
Beginning WIP Inventory Manufacturing Costs COGM Ending WIP Inventory. Some inventory might have one stage of machining done and other inventory might have all but one stage of machining done. Your manufacturer also produced 5000 pairs of shoes each costing around 30 to produce on average.
Part 1 of 3. WIP is a concept used to describe the flow of manufacturing costs from one area of production to the next and the balance in WIP represents all production costs incurred for partially completed goods. Definition formula and benefits.
How do you calculate work-in-process inventory. The calculation of ending work in process is. The beginning WIP inventory is a type of carryover from the last accounting periods balance sheet.
Raw Materials Direct Labor Costs Manufacturing Overhead Manufacturing Costs. The calculation is your cost of goods sold COGS plus your ending inventory balance minus your cost of purchasesIf you dont have an ending inventory balance to include simply subtract your cost of purchases. As a result this raises the price of manufactured items.
The current cycles beginning WIP inventory cost should be the exact same as the last cycles ending WIP inventory cost. The value of your businesss inventory is constantly changing as products are received assembled stored and sold. The quantity of work in process inventory on hand causes the manufacturing cost to increase.
The more WIP inventory that goes through the production process the higher the raw materials and labor costs will be which will impact the total costs of manufactured goods. The labor costs for the accounting period should be calculated. Force can be calculated with the formula Work F D Cosineθ where F force in newtons D displacement.
Inventory accounting is an important aspect of your fulfillment process because the cost of buying and storing a product is a major factor in your asset. This product value is important for financial reporting. An important note to consider is that work in process inventory can vary greatly.
100000 150000 150000 100000. WIP inventory is considered an inventory asset and as it moves through the stages of production it becomes part of the cost of sales. The factory overhead costs can be calculated for the accounting period.
The value of that partially completed inventory is sometimes also called goods in process on the balance sheet particularly if the company is manufacturing tangible items rather than providing services. As per the Merriam-Webster dictionary Work-in-process WIP refers to a component of a companys inventory that is partially completed. It is generally considered a manufacturing best practice to minimize the amount of work-in-process in the production area.
Cost of manufactured goods. Work in process WIP inventory refers to materials that are waiting to be assembled and sold. The beginning WIP inventory cost refers to the previous accounting periods asset section of the balance sheet.
The work-in-process inventory that a company has started but not completed has specific value. Beginning WIP Manufacturing costs - Cost of goods manufactured. As determined by previous accounting records your companys beginning WIP is 115000.
Yes work in process WIP inventory is considered inventory.
Explain And Demonstrate The Impact Of Inventory Valuation Errors On The Income Statement And Balance Sheet Principles Of Accounting Volume 1 Financial Accounting
Use The Job Order Costing Method To Trace The Flow Of Product Costs Through The Inventory Accounts Principles Of Accounting Volume 2 Managerial Accounting
Work In Progress Wip Definition Example Finance Strategists
Ending Work In Process Double Entry Bookkeeping
Inventory Formula Inventory Calculator Excel Template
What Is Inventory Turnover Inventory Turnover Formula In 3 Steps
What Is Work In Process Wip Inventory How To Calculate It Ware2go
Inventory Formula And Calculator Excel Template
Work In Process Wip Inventory Youtube
Inventory Formula Inventory Calculator Excel Template
Inventory Formula Inventory Calculator Excel Template
Inventory Formula And Calculator Excel Template
Ending Inventory Formula Calculator Excel Template
Calculate The Cost Of Goods Sold And Ending Inventory Using The Periodic Method Principles Of Accounting Volume 1 Financial Accounting
Methods Of Estimating Inventory Accountingcoach
Work In Process Inventory Formula Wip Inventory Definition
How To Calculate Ending Inventory Using Absorption Costing Online Accounting
What Is Work In Process Wip Inventory How To Calculate It Ware2go